When you turn to a Machine Tool manufacturer to evaluate a new plant, there are some features that you have to consider to understand the reliability of the manufacturer and of the machinery he will propose to you.
The starting point is absolutely to define your production goals, and then think about the correct choice and the machinery that best suits your needs.
As I continue to repeat, the Machine Tool is only a means, it is not the end.
It is a means that you use to achieve specific goals.
Thereby, I’m not saying that the machinery is not important or that it is not relevant for your final results. Quite the opposite!
But, first of all, you have to work in terms of objectives, then move on to a precise evaluation of the manufacturers of CNC Machine Tools.
Remember, it’s you who must know where you want to go, it’s not the manufacturer.
Once you have defined the production aims that you would like to achieve, you can move on to the research and consultation of the different Machine Tool manufacturers.
To do this, you must have some criteria that give you a yardstick and allow you to make tangible comparison.
In our case, we have identified 7 precise rules, that reflect our philosophy, and that we consider as the 7 COMMANDMENTS to apply to produce unique Machine Tools, that can guarantee our customers excellent results.
All our PORTACENTER machines are produced following these commandments, without exception.
And I believe that if you also want to achieve outstanding results, you should always ensure compliance with these 7 rules, because each one of them can make a big difference.
THESE ARE THE 7 COMMANDMENTS ON WHICH THE PORTACENTER IS BASED
1) RIGIDITY
This is the first commandment.
Considering that in 2000 the topic of rigidity stopped, or better sank, one of our flexible machine plans (the one with the revolver heads), our experience led us to choose this one as our starting point.
We made a list of basic concepts that we could not ignore to ensure the rigidity of our machines.
To be able to work a piece in the most rigid conditions, with any machinery, you have to:
- PLACE THE WORK PIECE AS NEAR AS POSSIBLE TO THE PALLET, avoiding multi-laying equipment, where Physics teaches that the higher you go up, the more instability is introduced due to the leverage effect.
- HAVE COMPACT TOOL HOLDERS, ONCE AGAIN TO SUPPORT RIGIDITY. Usually, with multi-laying pallets it is necessary to lengthen the tool holders in order to reach the work piece on the sides.
Only with these two points, even a machining center could improve the rigidity of the piece (positioning only one piece per pallet) and consequently, thanks to the single piece, the tool holders can be compacted to obtain more rigidity.
The problem is that no one applies this method because, by clamping a single piece on the pallet, productivity would collapse to such an extent that I would need so many machining centers to make the investment impossible, even in terms of space.
So, I can say that the equipment and tools that I often see implemented on standard machining centers, are a bad technical compromise to obtain an acceptable level of productivity.
Generally speaking, German or Japanese machining centers are technologically excellent machines, with very advanced performance, but they are equipped with poorly developed locking systems and long and unstable tools.
Making a comparison, it’s like having a high-performance Ferrari with its rims but without its tires … it’s all for nothing!
In this case, the machining center is the Ferrari, while the equipment and the cantilever tool holders are the rims without tires.
Often, visiting customers frustrated about that, I explain to them that the problem is not who produce the machine and that, in 90% of cases, who developed the equipment and tools is responsible for that.
2) FLEXIBILITY
This is the second commandment.
Flexibility in terms of the number of tools available, not only 6 as on the revolver heads, but 24 tools for each machining module, for a total of 72 tools.
This leads to two main advantages:
- Having more tools for each module allows you to better balance the cycle time between the modules.
- Having more tools allows you to leave the tools assembled for different products so that changes are faster, limiting just to the 4 workpieces.
You must therefore make sure that this point is also implemented.
3) PRODUCTIVITY
This is the third commandment.
In order to respect the first and the second commandments, which are fundamental for working a piece rigidly and safely, without “killing” productivity, in our case we have chosen to have 3 spindles, in order to divide the workload between them and be productive without affecting the clamping system and tool holders.
4) ONE PROCESS
Here is another important commandment, the fourth, whose value, at first sight, is not always clear.
Having 3 machining centers that produce the same piece simultaneously, means having 3 independent processes, so the capability of your machine will be the average of the CPK values of the 3 machines.
On the contrary, in our case, the PORTACENTER has 3 machining modules but, working in series and not simultaneously, the process is one, so I get one CPK value.
I would like to make a clarification in relation to bi-spindle or four-spindle machines: even in this case the processes are two or four and you will get two or four CPK values from which you will have to calculate the average.
What does it mean?
It means that with different processes, it will be much more difficult to obtain the CPK value, spending much more energy, requiring much more specialized operators and resorting to more expensive measuring systems that must be put in parallel.
In the case of “pushed” CPK values, you may not be able to get them through multiple processes, thing you would do more easily with a single process.
Through this reasoning, we have come to define our machine as follows:
PORTACENTER
1 Process, 3 Times Faster!
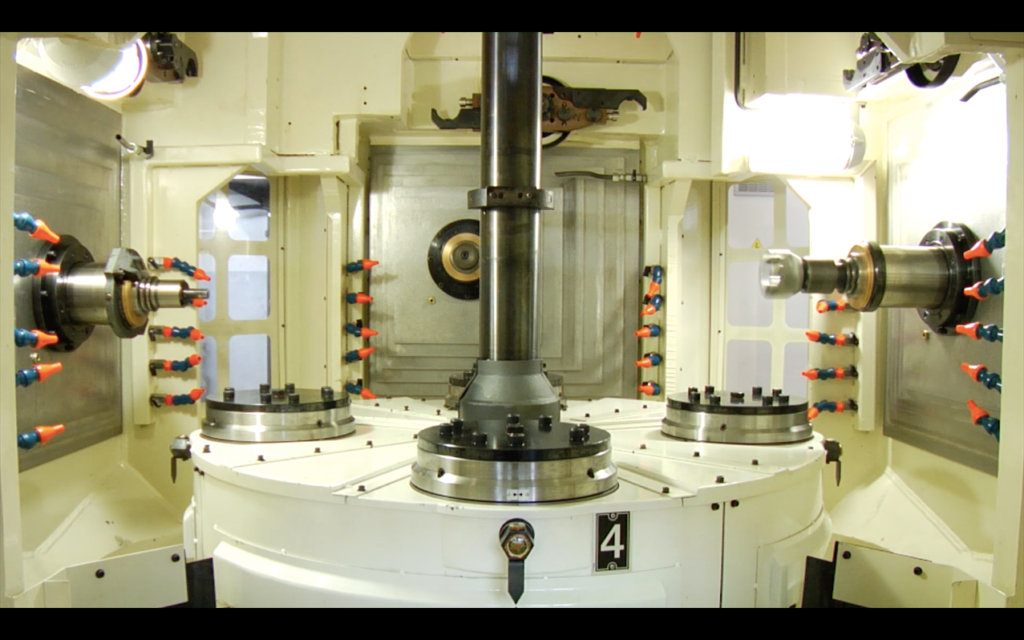
CLICK HERE to watch the video of 3 independent spindles
in 1 single process.
5) COST OF MACHINE
The fifth commandment is very important. First of all, there must be the proper technique to be translated in the market prices.
In order to satisfy this point, after various studies, we came to the conclusion that to propose an acceptable market value, the only way would have been to start series production, as the manufacturers of machining centers have been doing for years.
In 2005, we started to produce the first machines in series, even if at the beginning the effort was not enough, that’s why we committed ourselves to partially redesign our machines, implementing changes in order to reduce assembly times.
This was an important step that allowed us to experience, for the first time, the advantages coming from series production of machines.
From then on, the launch of the 6 machines became more and more frequent until it gets a monthly basis.
Today I can affirm that this commandment is fundamental when evaluating a Machine Tool manufacturer and his plants, because series production allows both you and the manufacturer to reach better agreements and cost advantages, impossible to obtain with prototypes and special transfer machines.
6) DELIVERY TIME
The sixth commandment concerns another aspect that is decisive towards our customer, namely optimizing deliveries considering his needs as much as possible and applying the best conditions.
Today the speed and the correct “timing” of implementation win, so it is very important for you to rely on a manufacturer that can guarantee delivery times in line with your production goals.
Thanks to series production and the development of a range of standard equipment, always in stock, if your case is part of this field of application, today we are able to schedule deliveries that vary from 30 to 60 days.
NOWADAYS
SPEED IS EVERYTHING…
… so having the right solution but not being able to offer it quickly or within your customer’s timeframe, is like not having the solution.
7) STANDARDIZATION
The seventh and last commandment is no less important than the others.
Relying on a manufacturer of special machines is like relying on an expert “technological tailor”, able to sew a tailor-made suit, according to the customer’s needs.
It could seem something good: the customer is satisfied in all respects, with a 100% customized project, just for what he needs.
So it seems …
But when we talk about special machines, we talk about “prototypes”, projects with low (or nothing) historical significance, which guarantee a much lower level of reliability than standard models, already tested several times.
It is therefore advisable to rely on a manufacturer who can also offer standard models.
In our case, the PORTACENTER has been perfectly standardized, to guarantee an incredible level of reliability and today these 7 commandments are carved in stone in our company.
Success hides behind complexity.
To choose the right manufacturer and the proper Machine Tool you have to make an accurate and scrupulous analysis, always taking these 7 rules into consideration.
With these concepts in mind, you can get an incredible advantage.
But remember, do not leave out even one, the long-term results are far more satisfying.
And, if you are a user of CNC Machine Tools for metalworking and you want to have a clear and more complete view for the evaluation of your next plant, just contact us.
ASK FOR A DIRECT CONSULTATION
with one of our Technical Tutors
Write to porta@flexible-production.com to get more information.
If you want to go deeper on the topics of
Flexible Production and Competitive Production
CLICK HERE
>>> www.flexibleproductionbook.com <<<
My book dedicated to users of Machine Tools who want to make the leap in quality, is waiting for you!!!
To your results,
Maurizio Porta
Master Trainer PORTA PRODUCTION METHOD